Magneti Marelli Software Rt3290
MAGNETI MARELLI DIAGNOSTIC SCAN TOOLS SPECIAL FUNCTIONS. Magneti Marelli’s diagnostic scan tools include monthly software updates and outstanding coverage for. VISION: Heading the Magneti Marelli product line up is their 'VISION' diagnostic scan tool. This is a self contained, hand held, multi-line scan tool that. Branson Series 8000 Manual here.
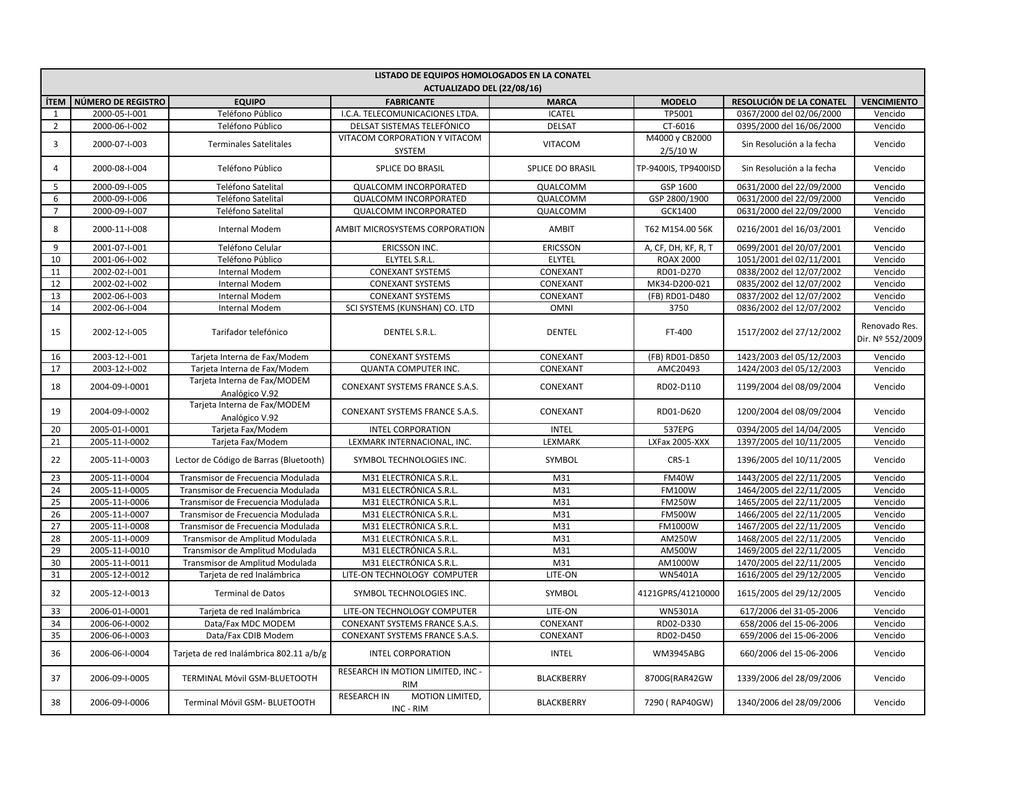
4 Magneti Marelli reviews. A free inside look at company reviews and salaries posted anonymously by employees.
Optimizing fuel injection systems The fuel injection system plays a key role in the reduction of vehicle fuel consumption and pollutant emissions. Gasoline and diesel direct injection engines require extremely reliable high-pressure injection systems for advanced combustion strategies and to improve the fuel atomization and air-fuel mixing processes. Nevertheless, in these installations the rapid opening and closing of the injectors and pump flow rate may cause fuel pressure fluctuations. These fluctuations can cause inferior precision, irregular fuel injections between cylinders and relatively poor spray quality. For this reason, the injection system design must be supported by accurate computational models able to predict the actual injector flow and the whole fuel system behavior. A worldwide automotive tier-one supplier, Magneti Marelli is providing its know-how and wide-ranging expertise in electronics through a process of ongoing innovation and environmental sustainability. The group wants to develop intelligent systems for active and passive vehicle safety, onboard comfort and powertrain technologies.
In 2009, Magneti Marelli chose, part of the SimcenterTM portfolio from Siemens PLM Software, to support the design process of its high-tech fuel injection components and systems for cars, motorbikes and light vehicles. Dao Of Chinese Medicine Pdf Download. “Model-based systems engineering is the only possible approach to deal with the actual complexity of injection system design,” says Domenico Paolino, mechanical engineer at Magneti Marelli. With LMS Amesim, Magneti Marelli precisely models multi-domain components of modern fuel injection systems in order to control the fuel pressure fluctuation, inject the exact amount of fuel into the combustion chamber and thus lower the fuel consumption and meet stringent emission regulations. Using LMS Amesim, engineers check the correct dimensions of the fuel system and the right positions for flow restrictors and dampers to enhance their effectiveness.
Supporting controls design Recently, the company developed a new technology, Controlled Low-Pressure Pump Supply (COLPS), to optimize its previous fuel system which included a pressure regulating valve (PRV) and fuel metering valves (FMVs). The injection system rail simplification enabled Magneti Marelli to reduce production costs. With COLPS, the low-pressure pump is controlled with an electric motor, which allows better control and pressure variation optimization. Moreover, the low-pressure pump can generate the exact flow rate to meet the target rail pressure with possible energy savings and emissions reduction.
Even though the injection system design was greatly simplified, the new technology requires a much more sophisticated controls strategy. To address controls complexity, Magneti Marelli system engineers use LMS Amesim to support the controls and software design teams that need to receive indications on hydraulic components’ behavior. Co-simulation with LMS Amesim and the environment enables the controls algorithm to communicate with a plant model at a fixed time step, as in a real engine control unit (ECU). “This approach enables us to assess in parallel hydraulic components and software behavior, which would be extremely time-consuming if performed directly on the test bench,” says Paolino. “Dealing with the validated hydraulic components of LMS Amesim enables the optimization of the software structure from the first design step. Puppy Love 2 The Spacening Download more.
Further advantages are those related to the simulation of possible mechanical failures and software malfunctions, which help us understand the effects on the system and thus give important information about all the diagnosis design.” Taking advantage of two simulation environments Magneti Marelli chose to develop its controls strategy with Simulink while using LMS Amesim to model the multi-domain engine components. The two solvers are in communication, and inputs and outputs are exchanged between the two environments.
The creation of a complete virtual system environment enables simulation of the system behavior, for both hydraulic components and software. LMS Amesim and Simulink work together to improve the reliability of the controls strategy. “We were able to match the advantages of these two environments to build complete model-based software including a multi-domain system built using LMS Amesim and controls model built using Simulink. It enables us to optimize the product and components design from the first stages,” says Paolino. Running virtual tests Using co-simulation, Magneti Marelli runs virtual tests that would be impossible to recreate in reality.